In the world of woodworking, where power tools and cutting-edge machinery often reign supreme, there exists a time-honored tradition that remains steadfastly committed to simplicity and tradition. The Amish, renowned for their rich heritage and distinctive way of life, have honed their woodworking skills for generations, employing techniques that embrace craftsmanship, patience, and the raw beauty of natural materials.
Amish woodworking encompasses a range of techniques that reflect their commitment to simplicity. Some Amish woodworkers’ well-known woodworking methods, especially in Amish furniture making, are hand tool utilization, joinery, steam bending, hand carving, and hand sanding/finishing.
Keep on reading to know more about these amazing Amish woodworking techniques.
A Closer Look At the Amish Woodworking Techniques
A remarkable blend of age-old techniques and a deep reverence for the natural world are the most prominent characteristics of Amish woodworking.
Rather than relying on modern machineries that require electricity, the Amish woodworkers utilize traditional manual techniques to shape and craft their wooden masterpieces, especially the popular Amish furniture. This is one of its notable differences compared to mass-produced furniture.
Here are some special techniques used by the Amish furniture makers, Amish carpenters, and Amish woodworkers in their woodcrafting endeavors:
Hand Tool Utilization
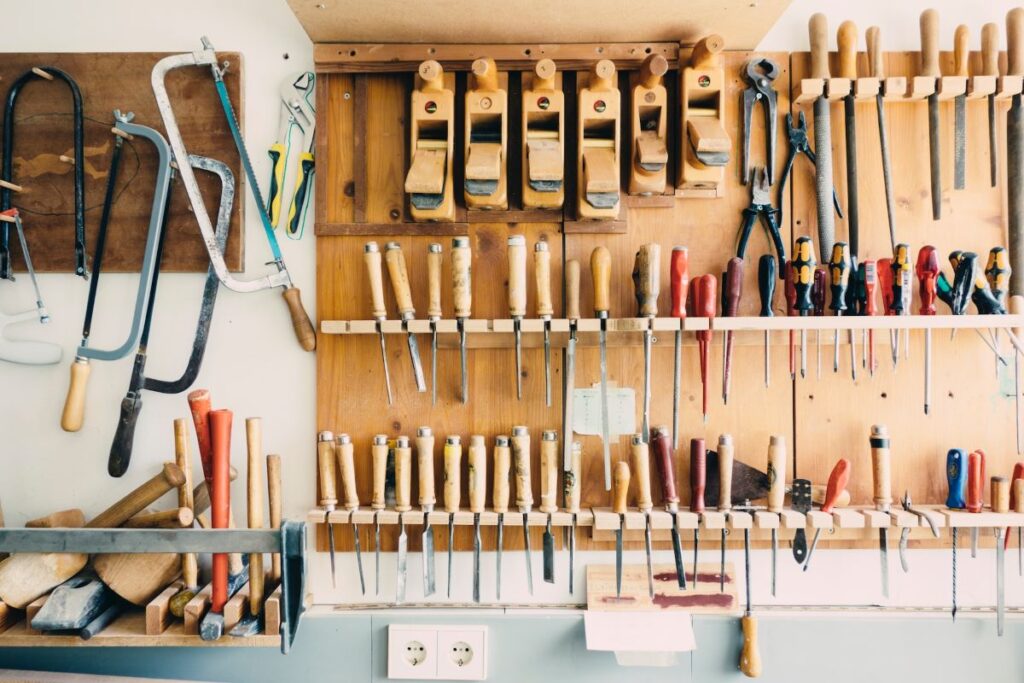
Learning woodwork can be tricky. The Amish furniture makers and Amish carpenters rely extensively on hand tools rather than power tools. They skillfully use planes, chisels, saws, and scrapers to shape, smooth, and refine solid wood surfaces.
This practice allows for greater precision and control while emphasizing the tactile connection between the Amish and the materials.
Hand Planes
Hand planes play a central role in Amish furniture making and woodworking. These versatile tools consist of a sharp blade housed in a wooden or metal body and a handle for gripping and controlling the plane.
Amish woodcrafters skillfully use planes to remove excess wood, flatten surfaces, and create smooth, even finishes. They can adjust the depth and angle of the blade to achieve specific cuts and shapes, allowing for meticulous control over the woodcrafting task.
Chisels
Chisels are another essential hand tool in Amish woodworking. The Amish use chisels to shape pieces of wood, remove material, and refine the contours of their creations.
These sharp-edged tools come in various sizes and shapes, enabling Amish crafters to carve out intricate details, make precise cuts, and create recesses or mortises for joinery.
Saws
Saws, such as hand saws and coping saws, are also widely utilized by the almost everyone in almost all Amish communities. These hand tools enable them to make accurate and controlled cuts, whether straight, cross, or intricate curved.
By guiding the saws manually, the Amish woodworkers can tailor the cutting process to their specific needs and achieve the desired level of precision.
Scrapers
Scrapers are used to smooth and level wood surfaces. These handheld tools consist of a thin metal blade carefully drawn across the wood, scraping away imperfections and leaving behind a polished finish.
Scrapers allow the woodworkers to achieve exceptional smoothness and refine the final appearance of their Amish craftsmanship.
Joinery
Joinery is a vital technique woodworkers from Amish communities employ to create strong, durable, visually appealing connections between wooden components without relying on nails or screws.
Amish joinery techniques are time-honored and often passed down through generations, contributing to the longevity and structural integrity of their woodworking projects.
Dovetail Joints
One commonly used joinery technique among the Amish is the dovetail joint. This type of joint involves interlocking trapezoidal-shaped projections, called tails, on one piece of wood with corresponding notches, called pins, on another part. The resulting joint is solid and resistant to pulling forces.
Dovetail joints are frequently used to construct drawers, cabinets, and many Amish furniture styles, especially the Amish “Mission Style” or “Shaker Style Furniture.”
Mortise and Tenon Joints
Another prevalent technique is the mortise and tenon joint. In this method, a rectangular slot, a mortise, is created in one piece of lumber, while a protruding portion, called a tenon, is formed on the mating piece. The tenon is inserted into the mortise, creating a secure and durable connection.
Mortise and tenon joints are often used in Amish furniture construction, framing, and architectural woodworking.
Tongue-and-Groove Joints
Tongue-and-groove joints are also popular among Amish woodworkers. This joint involves creating a long, protruding “tongue” on one solid wood piece and a corresponding groove on another. When assembled, the tongue fits into the groove, making a tight and seamless joint.
Tongue-and-Groove Joints are frequently used in flooring, paneling, and cabinetry construction.
You might want to learn if the Amish use wood glue in woodworking.
Steam Bending
Steam bending is a remarkable technique employed by Amish furniture makers and woodcrafters to shape wood into graceful curves and bends.
By subjecting wooden pieces to steam and carefully manipulating them, the Amish artisans can achieve complex and elegant forms that enhance the beauty and functionality of their woodworking projects.
The entire task of steam bending starts with selecting a suitable piece of wood, preferably one with elastic properties that can withstand the bending process without cracking or breaking. Commonly used wood species for steam bending include oak, ash, hickory, and walnut.
The wood is prepared by cutting it into long, thin strips or boards slightly wider than the desired final shape.
These strips are then placed in a steam box, a specially constructed chamber where steam is introduced to the wood. The steam box ensures the wood becomes pliable and easier to bend without causing damage.
The duration of the steam exposure depends on various factors such as wood species, thickness, and moisture content.
The Amish woodcrafters rely on their experience and judgment to determine the optimal time required for the wood to reach the desired level of flexibility. Typically, the wood is steamed for a period running from a few minutes to hours.
Once sufficiently steamed, the wood is carefully removed from the steam box and immediately placed into a bending form or jig.
The bending form is designed to hold the wood in the desired shape until it cools and dries, retaining the curved structure. The Amish woodworker skillfully manipulates the wood, using clamps, straps, or other tools to ensure even pressure and proper alignment during the bending process.
As the wood cools and dries, it hardens into the new curved shape, permanently retaining the desired form.
The steamed and bent wood can then be refined through additional woodworking techniques such as hand planing, sanding, and finishing, achieving a smooth surface and enhance its overall appearance.
Steam bending allows the Amish to craft unique and fluid designs that incorporate organic curves, enhancing the aesthetic appeal of their furniture, architectural elements, and other woodworking projects.
It showcases their mastery of materials and ability to shape wood in visually captivating and structurally sound ways.
Hand Carving
Hand carving is a unique and intricate technique within Amish furniture making and other woodcrafting projects that involves the skilled manipulation of wood through carving tools to produce decorative elements, intricate patterns, and intricate designs.
This technique allows Amish furniture makers to add a personal touch and intricate details to their wooden creations, be it Amish chairs or tables, showcasing their artistic expression and craftsmanship.
Amish hand carving typically starts with a carefully selected piece of wood suitable for carving. The wood’s grain, density, and texture are considered to ensure optimal carving results. Commonly used wood for hand carving include cherry, walnut, oak, and maple.
The job begins with the artisan sketching or transferring the decorative details onto the wood’s surface using a pencil or a tracing instrument. They then select the appropriate carving tools, which include gouges, chisels, knives, and V-tools, each serving a specific purpose in the carving task.
Using these tools, the Amish artisan methodically removes layers of wood, following the design outlines and creating depth, texture, and intricate patterns.
They employ various carving techniques, such as relief carving, in which the design is raised from the wood’s surface, or incised carving, where the design is cut into the wood.
The artisan’s skill and expertise carefully control the depth and detail of the carving. They may use gouges to remove larger wood sections, chisels, or knives for finer details and delicate areas.
The process requires patience, precision, and a deep understanding of the wood’s grain and properties to achieve the desired result.
Hand Sanding and Finishing
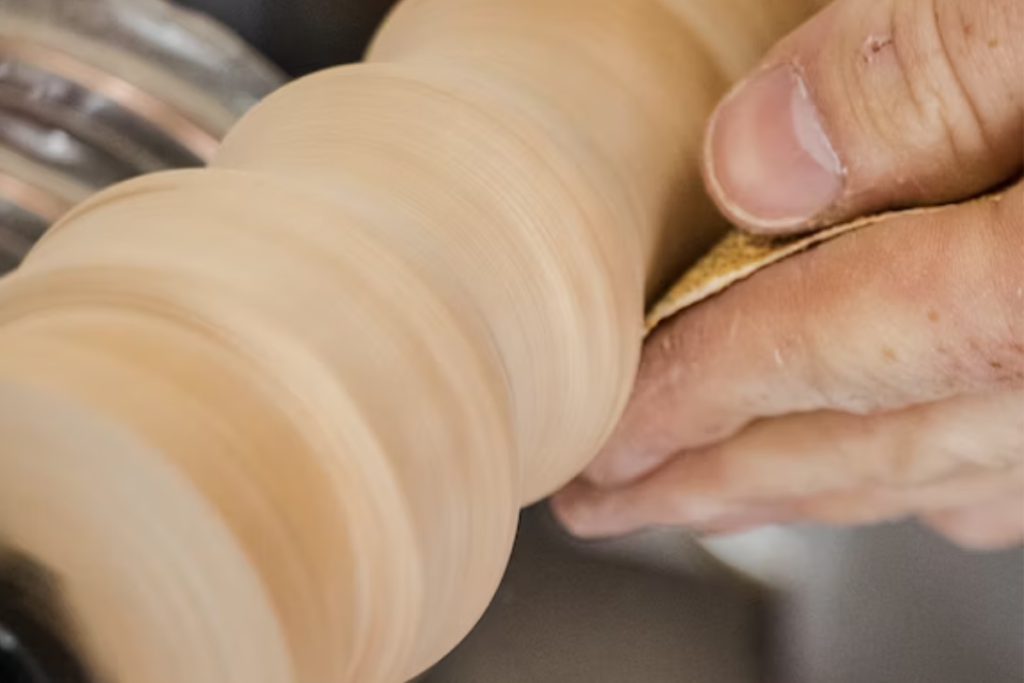
Hand sanding and finishing is a crucial stage in Amish wood crafting. It involves refining the wood’s surface through careful sanding and applying various finishing techniques to enhance its appearance and protect it from wear and tear.
This meticulous technique ensures a smooth, polished finish that accentuates the wood’s raw beauty while showcasing the artisan’s attention to detail.
The hand sanding task begins after the woodworking piece has been shaped, carved, and assembled.
Amish woodworkers start with coarse-grit sandpaper to remove rough surfaces, imperfections, or tool marks. They gradually progress to finer-grit sandpaper, working through various grits to achieve a smoother finish.
During sanding, the woodworker applies even pressure and uses smooth, consistent strokes along the wood grain. This technique prevents the creation of uneven or scratchy surfaces while preserving the integrity of the lumber’s natural patterns and texture.
As the sanding process continues, the woodworker double-checks the surface carefully, feeling for any remaining imperfections or inconsistencies.
They may use handheld sanding blocks or wrap sandpaper around various tools, depending on the size and shape of the piece, to achieve precise results.
Once the desired smoothness is achieved, the Amish woodworker moves on to the finishing stage. Finishing techniques vary but often involve applying natural oils, waxes, or shellac to the wood’s surface.
These finishes enhance the wood’s color, protect it from moisture, and provide a lustrous sheen.
The choice of finishing product depends on the desired outcome and the wood species being used. Some finishes, such as linseed or tung oil, penetrate the fibers, enriching the color and offering a natural, matte appearance.
Other finishes, like varnishes or lacquers, create a protective layer on the surface, providing a glossy or satin finish.
The Amish woodworker carefully applies the chosen finish, ensuring even coverage and sufficient drying time between coats. They may use brushes, rags, or even their hands to apply the finish, depending on the size and intricacy of the piece.
If you’re interested, you might want to read how Amish furniture is different from Chinese-made furniture.
Conclusion
The Amish woodworking tradition, together with the world-renowned Amish furniture, is a testament to the enduring power and quality of Amish craftsmanship and the deep connection between artisans and their materials.
Through their unwavering dedication to hand tool utilization, joinery techniques, steam bending, hand carving, and meticulous hand sanding and finishing, the Amish have sharpened their woodworking skills to build furniture and even homes that are considered by many as timeless pieces of artistry, such as the popular Amish furniture that are proven to last for many generations.
The commitment of every Amish community to simplicity, tradition, and the inherent beauty of natural materials is evident in each meticulously crafted wooden creation.
By embracing these techniques and preserving their woodworking heritage, the Amish continue to inspire us with their ability to transform humble pieces of wood into enduring works of art that captivate the eye and touch the soul.
You also might want to read more on Amish people and their mattresses at home.
Tags: Woodworking